Hexagon Manufacturing Intelligence’s new CAM programming tool ProPlanAI, powered by Microsoft’s Azure OpenAI cuts time needed to program factory machines.
Hexagon’s Manufacturing Intelligence division has unveiled ProPlanAI, brand-new automated computer-aided manufacturing (CAM) programming tool.
This phenomenal tool, powered by Microsoft’s Azure services integrated into Hexagon’s cloud-based Nexus, reduces the time taken to program factory machine tools by 75%.
Providing profound new levels of connectivity and collaboration for discrete manufacturers, this advanced AI technology constitutes the next step in CAM evolution.
ProPlanAI was presented at the Microsoft Ignite Conference in Chicago, USA as a solution that will help manufacturers of any size apply institutional knowledge more easily, quickly and thoroughly through AI.
Enabling operational excellence at scale, the tool is due for a public launch in Q1 2025.
“In a highly competitive market, productivity on the factory floor is crucial,” says Chuck Mathews, General Manager for Production Software at Hexagon.
“While many machines are now automated, the programming of them is often long and laborious and requires highly-skilled professionals that are spread thinly.”
“We have collaborated with Microsoft to leverage their powerful AI capabilities through Nexus, so manufacturers can boost productivity by allowing their programmers to focus on complicated tasks where their knowledge has the greatest impact.”
“Because manufacturers use their own pool of data to build programmes, suggestions automatically reflect the knowledge and experience of individual businesses, as well as the parts they produce and the machine tools they use. This ensures that new staff members can be quickly brought up to speed, while also ensuring that there is no knowledge drain when a person leaves a company or retires – something that is vital in an industry facing a skills shortage.”
The value of AI to CAM programmers
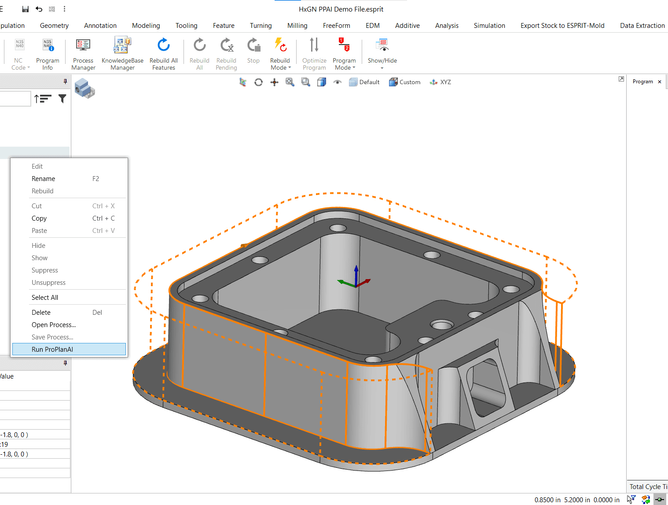
ProPlanAI works by learning from the data created by a manufacturer’s CAM programmers.
As the AI learns from this data it can predict ideal outcomes, tailored to a company’s unique preferences, needs and production capabilities.
Powered by Nexus and available within Hexagon’s popular desktop CAM software, this learning and adaptation is the key to enhancing productivity and efficiency on a broader level.
Before AI, CAM programmers could spend anywhere between an hour to several days determining the best strategy to CNC machine a new component.
This is due to all the steps involved, which include selecting correct tools, workholding and toolpath strategies as programmers evaluate thousands of potential approaches and variables.
With AI manufacturers shorten lead times and raise productivity, leading to higher volumes of work far more quickly.
Experienced programmers are freed up to focus on more complex, higher impact tasks while junior employees progress quicker and develop greater productivity.
All of this helps to address manufacturing’s ongoing digital skills gap.
ProPlanAI: the features
ProPlanAI can be trained using the manufacturer’s institutional knowledge, freeing up expert staff whilst ensuring machines are efficiently and quickly programmed to their quality standards.
The Hexagon copilot provides users with valuable tips, suggested pathways and tailored advice on best practice without users needing to leave their CAM software.
The programming of machine tools can be entirely automated, improving productivity and streamlining the design and engineering process.
In addition to this streamlining, ProPlanAI will help manufacturers identify latent standard practices by providing notifications about deviations from company programming standards.
The tool also better utilises product manufacturing information (PMI) embedded in design files to enhance the automation of CNC even further.
ProPlanAI also features AI-powered chat support that guides users through the process of setting up and programming a machine.
This feature, along with the others above, has already been beta tested by several industry experts.
These include RODIN Machining, which is on a journey towards complete unmanned production for milling, turning, gripper and material handling, loading and unloading machines, and tool change.
“We set out to build the first autonomous factory in 2022 and we make extensive use of automation, but machine tool programming is complicated and it requires experience,” says Paul Mooij, Director of Digital, RODIN machining.
“What makes ProPlanAI exciting is that we can leverage our human capital to achieve greater machine utilisation – our team can program machines in a fraction of the time by applying their valued skills in supervising ProPlanAI suggestions and finalising the programme specifics.”
Hexagon & Microsoft: partnering on software innovation
ProPlanAI is the result of ongoing strategic collaboration between Hexagon and Microsoft, as both companies seek to redefine the future of software-led manufacturing.
Central to this are their innovations in cloud technology, which primarily center on Azure and Hexagon’s connectivity cloud platform Nexus.
Hexagon also sponsors Microsoft Ignite 2024, which is currently ongoing in Chicago.
Microsoft’s passion for AI and software integration in manufacturing is well known, with the technology leader recently announcing its new AI models for industry.
Both companies continue to seek new ways to use digital tools to enhance manufacturing efficiency and critically, productivity.
“Microsoft’s collaboration with Hexagon is driven by a shared belief that we can transform manufacturing productivity,” says Clare Barclay, President, Enterprise and Industry, Microsoft EMEA.
“It’s rewarding for us to see how the AI capabilities provided by Azure are empowering expert CNC programmers with productivity-boosting automation, while also helping new users to upskill faster.”
“This is exactly the sort of transformation AI can bring to the industry, and we are excited to see Hexagon apply its manufacturing expertise to transform workplace productivity throughout the value chain with its Nexus platform.”