Lockheed Martin, Boeing and Spirit Airlines are embracing bend-forming to enhance their approach to engineering and revolutionise space manufacturing
Bend-forming is transforming the aerospace industry, enabling manufacturing leaders to produce complex, high performance components with greater precision and efficiency.
In an industry where guaranteed reliability, performance and safety is paramount, bend-forming enables companies to meet strict requirements whilst pushing the boundaries of innovation.
Here’s what this engineering technique is, how it works and three manufacturers that are taking it to new heights.
What is bend-forming?
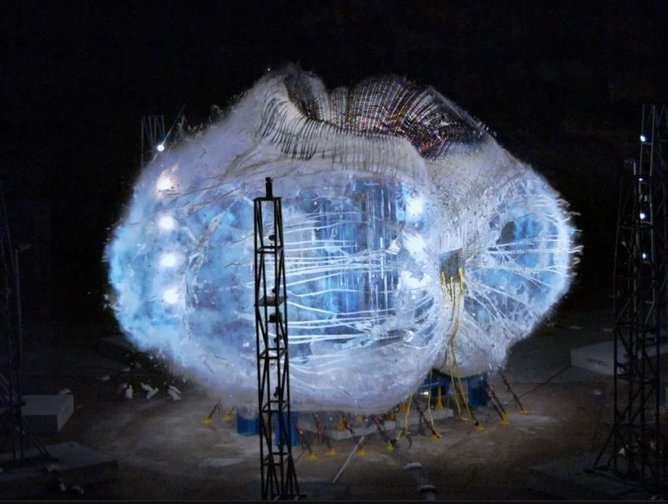
Bend-forming involves shaping materials- typically metals- into precise, curved geometries without compromising their structural integrity.
Using specialised machines manufacturers will apply force to metal sheets, rods, or other forms to bend them into predetermined shapes.
This technique is invaluable for creating durable yet lightweight components that meet stringent aerospace applications.
NASA has been fabricating its high-performance reflectors in space through bend-forming.
“In this NIAC effort, we aim to overcome this limitation by using a novel in-space manufacturing method and advanced materials to fabricate high-performance reflectors with dimensions greater than 100 m, 100 m/m surface precision, and specific area in excess of 10 m2/kg,” Zachary Cordero, Associate Professor from the Massachusetts Institute of Technology explains on NASA’s website.
“The structures enabled by the proposed approach will benefit a wide range of spaceflight activities, from sensing and comms, to emerging solar sail and power generation technologies.”
The organisation has opted for this method as it is more operationally robust, produces less heat and requires less power than alternative in-space manufacturing and assembly approaches.
Bend-forming also minimises material loss, unlike traditional methods like machining which generate waste and remove material.
This method also has less demanding assembly needs, as components can often be formed in a single piece, improving structural strength and lowering manufacturing costs.
Manufacturers across aerospace and aviation have adopted bend-forming, including influential leaders Boeing, Lockheed Martin and Spirit AeroSystems.
How Boeing uses bend-forming
Boeing, one of the world’s largest aerospace manufacturers, utilises bend-forming extensively in its production lines.
This is especially prominent with the company’s commercial aircraft, where bend-forming is instrumental in shaping the aluminium and titanium components used in airframes, wings, and fuselage sections.
In modern aircraft like the Boeing 787 Dreamliner, bend-forming contributes to the design of lightweight yet robust parts.
The Dreamliner’s structure relies heavily on advanced materials such as titanium and composites, which can be more easily transformed into precise aerodynamic shapes through bend-forming.
This precision helps improve fuel efficiency and performance, crucial as the manufacturer seeks to reduce operating costs and carbon emissions.
Boeing has also automated its approach to bend-forming, utilising robotic systems to enhance precision even further.
This enables the manufacturer to streamline production whilst ensuring its safety-critical components meet requirements.
Lockheed Martin: bend-forming for defense
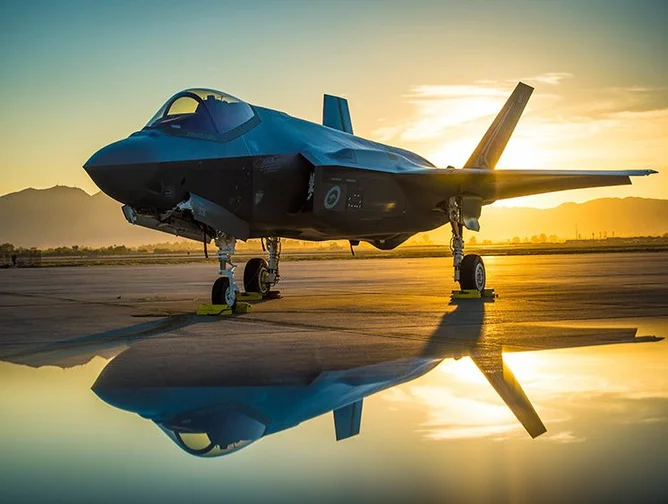
Lockheed Martin, another leader in defense and aerospace manufacturing deploys bend-forming across its production processes.
These include in its manufacturing of advanced military aircraft like the F-35 Lightning II.
Bend-forming enables Lockheed Martin to deliver superior performance in high-stress environments.
Its aircraft destined for military deployment must be capable of enduring extreme thermal conditions and performing high-speed manoeuvres for military deployments.
Bend-forming enables this through allowing high-strength alloys like titanium and nickel-based superalloys to be shaped into components that meet these demanding specifications.
this technique is also critical to the production of stealth aircraft.
The precise shaping achieved through bend forming contributes to reduced radar cross-sections, a key feature of stealth technology.
Spirit AeroSystems: optimising supply chains
Spirit AeroSystems, the leading supplier of aerostructures leverages uses bend forming to meet the demands of Boeing, its owner.
The company was acquired by Boeing earlier this year in July, in a US$8.3bn ac
The manufacturer must produce fuselages, wind components and nacelles that align with stringent weight, strength, and aerodynamic requirements.
Spirit AeroSystems’s approach to bend-forming is augmented with advanced tooling and simulation software. This approach helps optimise the bend-forming process, ensuring consistent quality and reducing time needed for prototyping and making adjustments.
By predicting material behaviour during forming, engineers can minimise defects such as springback, a common challenge in bending high-strength materials.
Spirit AeroSystems’s investment in bend-forming also enhances its ability to scale production while maintaining cost efficiency.
By using this method to produce large, integrated components, Spirit AeroSystems reduces the need for extensive assembly, speeding up delivery time and strengthening the supply chain.
Fuelled by collaboration & innovation
The adoption of bend-forming by Boeing, Lockheed Martin, and Spirit AeroSystems highlights its importance in modern aerospace manufacturing.
This technique enables manufacturers to more easily meet stringent aviation and aerospace requirements, reducing weight, improving fuel efficiency, and enhancing performance in the process.
As the aerospace industry continues to push boundaries, collaboration between manufacturers, suppliers, and research institutions is driving innovation in bend-forming.
Advances in materials science, simulation software, and automation are further refining the process, enabling even greater efficiency and accuracy.
By integrating bend-forming into their operations, Boeing, Lockheed Martin, and Spirit AeroSystems are not only enhancing their manufacturing capabilities but also setting new benchmarks for the aerospace industry.